High pressure rubber seals are integral components in various industries, ensuring the integrity and safety of mechanical systems. With the demands for efficiency and reliability rising, understanding the nuances of these seals is crucial for industry professionals and engineers.
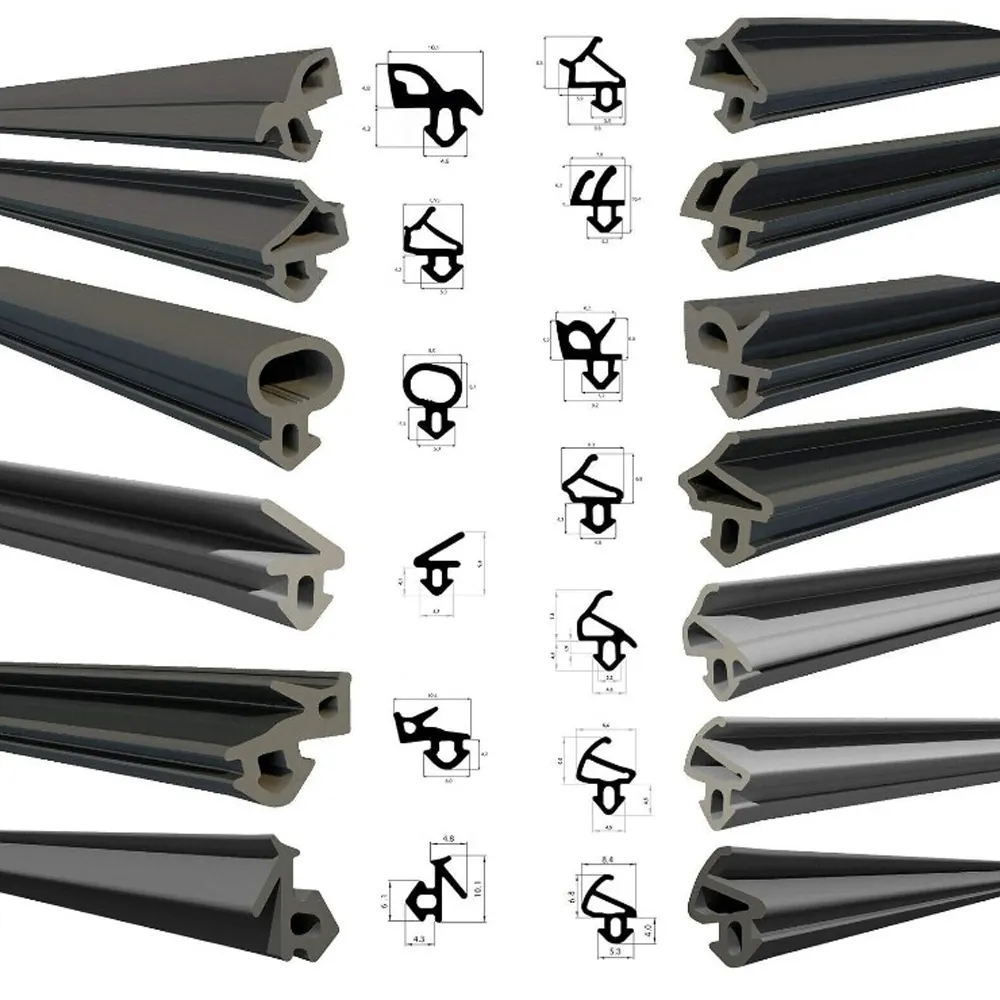
High pressure rubber seals are primarily used to prevent leaks and maintain the pressure of liquids and gases within systems, such as pipelines, engines, and hydraulic systems. They are crafted from robust materials, usually synthetic rubbers like nitrile, Viton, or EPDM, each offering unique properties suitable for different applications. For instance, nitrile is favored for its excellent resistance to petroleum-based fluids, whereas EPDM excels in outdoor applications due to its superior weather-resistant properties.
Choosing the right high pressure rubber seal involves comprehending a system’s specific requirements, including pressure, temperature, and the nature of the fluids being sealed. Engineers must consider these factors meticulously to ensure that the seal offers optimal performance without compromising safety. This requires a profound understanding of material science and engineering principles, emphasizing the expertise required to optimize seal performance for longevity and efficiency.
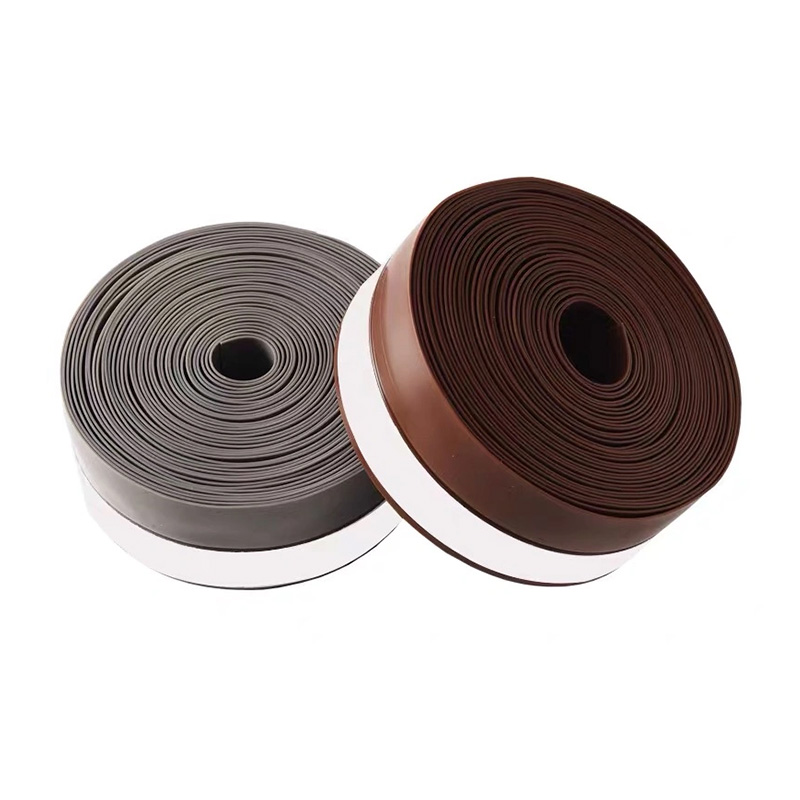
There are several critical advantages to using high pressure rubber seals. Their elasticity allows them to maintain contact with sealing surfaces despite fluctuations in temperature and pressure. This adaptability ensures that systems can operate under varying conditions without risk of failure. Moreover, the durability of rubber seals minimizes the need for frequent replacements, ensuring cost-effectiveness and reliability over time.
Experience drawn from real-world applications highlights common challenges faced in the selection and maintenance of these seals. One primary challenge is material degradation due to exposure to harsh environments or chemical interactions. This can lead to seal failure, resulting in leaks that could shut down operations, cause damage, or pose safety risks. Addressing such issues involves thorough material testing and routine inspections—a practice backed by authoritative industry standards.
high pressure rubber seals
Trust in high pressure rubber seals is reinforced by adherence to these standards, which delineate specifications for both manufacturing and application processes. Organizations such as the American Society for Testing and Materials (ASTM) provide guidelines that ensure seals meet rigorous quality and performance criteria. By following these guidelines, manufacturers and end-users can establish a trustworthy relationship, knowing that the seals used are reliable and compliant with international safety standards.
Innovation in the field of high pressure rubber seals is driving forward their performance capabilities. With advancements in material science, new compounds are being developed that enhance resistance to extreme temperatures and aggressive chemicals. These enhancements increase the seals’ applicability across different sectors, from automotive to aerospace, where extreme conditions are common.
In terms of expertise, leveraging advanced simulation tools allows engineers to predict seal performance under varying conditions, thus tailoring solutions to precise operational needs. Computational fluid dynamics (CFD) and finite element analysis (FEA) are commonly employed to visualize how seals will behave within a system. This predictive capability not only aids in designing more effective seals but also considerably reduces the time and cost associated with physical prototyping.
Emerging trends in the industry point towards environmentally friendly practices, encouraging the development of seals that are not only efficient but also sustainable. Researchers are experimenting with biodegradable materials and eco-friendly manufacturing processes. These innovations strive to balance performance with environmental impact, ensuring that high pressure rubber seals meet the demands of a rapidly changing world.
In conclusion, high pressure rubber seals are vital components that ensure the proper functionality of high-pressure systems. Their importance spans various industries, demanding expertise and a deep understanding to address unique engineering challenges confidently. As advancements continue, these seals will become more efficient, environmentally friendly, and tailored to sustain the ever-evolving demands of modern industrial applications. Investing in high-quality seals and routinely evaluating their performance are critical steps in maintaining system integrity and efficiency, establishing a solid foundation of trustworthiness and reliability.