China’s LIB Manufacturing Processes, based on findings from Huaxi Securities.
- Coating machines account for 80% of capital expenditure in front end. (Total capex RMB60–80 million/GWh)
- Winding/stacking machines account for 70% of capital expenditure in middle end. (Total capex RMB60–80 million/GWh)
- Cell Formation and ageing account for 70% of capital expenditure in back end. (Total Capex RMB60 million/GWh)
- Cell chemistries have more to do with front end electrode fabrication.
-
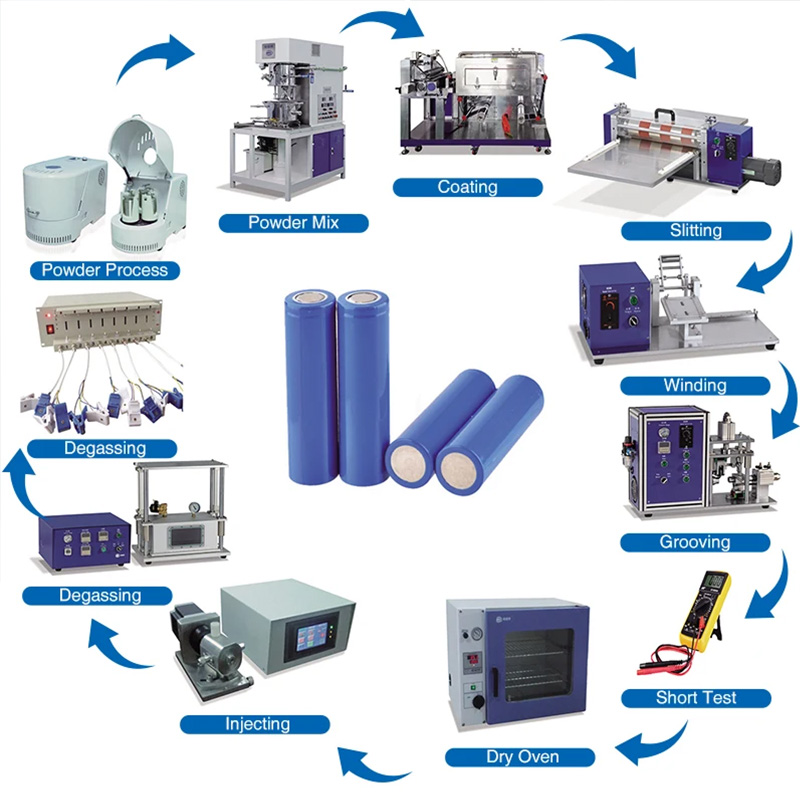
- Cell Formats have more to do with middle end cell assembly.
- Different packing (cell-to-pack CTP/blade batteries) have more to do with back end cell packing.
Technological innovation to increase efficiency and lower costs.
- Integrating several processes into 1 complex machinery
- This increases manufacturing efficiency, measured in terms of productivity per minute (PPM), accuracy and production yield.
- Technological innovation achieving tighter-packed electrodes and reducing battery burr. (See winding and packing technologies below).
- Expanding production volume also plays a key role in battery cost reduction. Batteries Journal (2022) argues that economies of scale can achieve 31% reduction in cell production cost.
- Labour cost is one of the most important factor of difference in total cell production cost (ex. material costs). This is driving automation within LIB manufacturing processes.
- E.g. Labour costs in Poland contributes to US$6/kWh to total cell costs while labour costs in Germany contributes US$25.6/kWh.
- Location also varies the production cost, varying from US$106.4/kWh in China to US$153.6/kWh in Norway. (dollar amounts referring to total cell cost).
- Energy cost differential also makes a difference. Industrial electricity cost for cell production in Sweden is US$1.4/kWh. That value is US$6.9/kWh in Germany.
End of Bullet-point summary. Below is a detailed deep-dive into LIB cell manufacturing.