When discussing the integral components of modern engineering and manufacturing, silicone rubber seals often emerge as a key topic due to their unmatched versatility and utility. Offering a unique blend of properties that cater to a wide variety of industrial applications, silicone rubber seals stand as a testament to engineering ingenuity.
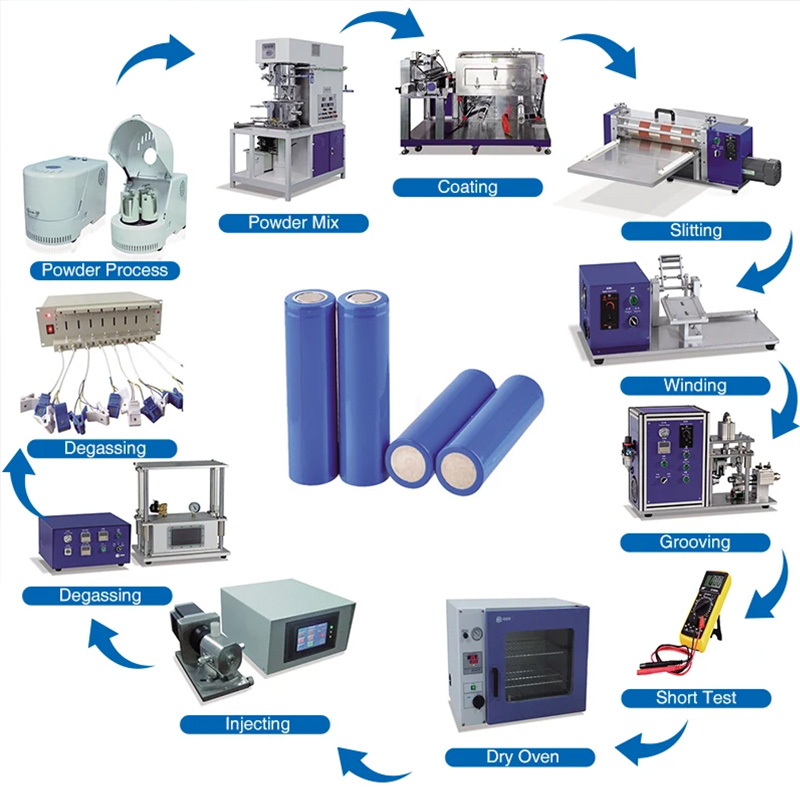
Silicone rubber seals are renowned for their exceptional resilience and durability, making them highly valued in industries such as automotive, aerospace, healthcare, and electronics. One of their most revered attributes is their ability to withstand extreme temperatures, ranging from as low as -60°C to as high as 230°C. This temperature resistance empowers manufacturers to deploy these seals in environments that would otherwise compromise the integrity of less robust materials.
Another compelling feature of silicone rubber seals is their superior chemical resistance. Unlike seals made from natural or synthetic rubber, silicone variants maintain their chemical stability when exposed to a wide spectrum of elements, including oils, solvents, and other potentially corrosive substances. This chemical resistance is crucial in automotive and aerospace applications, where exposure to harsh fluids is a routine occurrence.
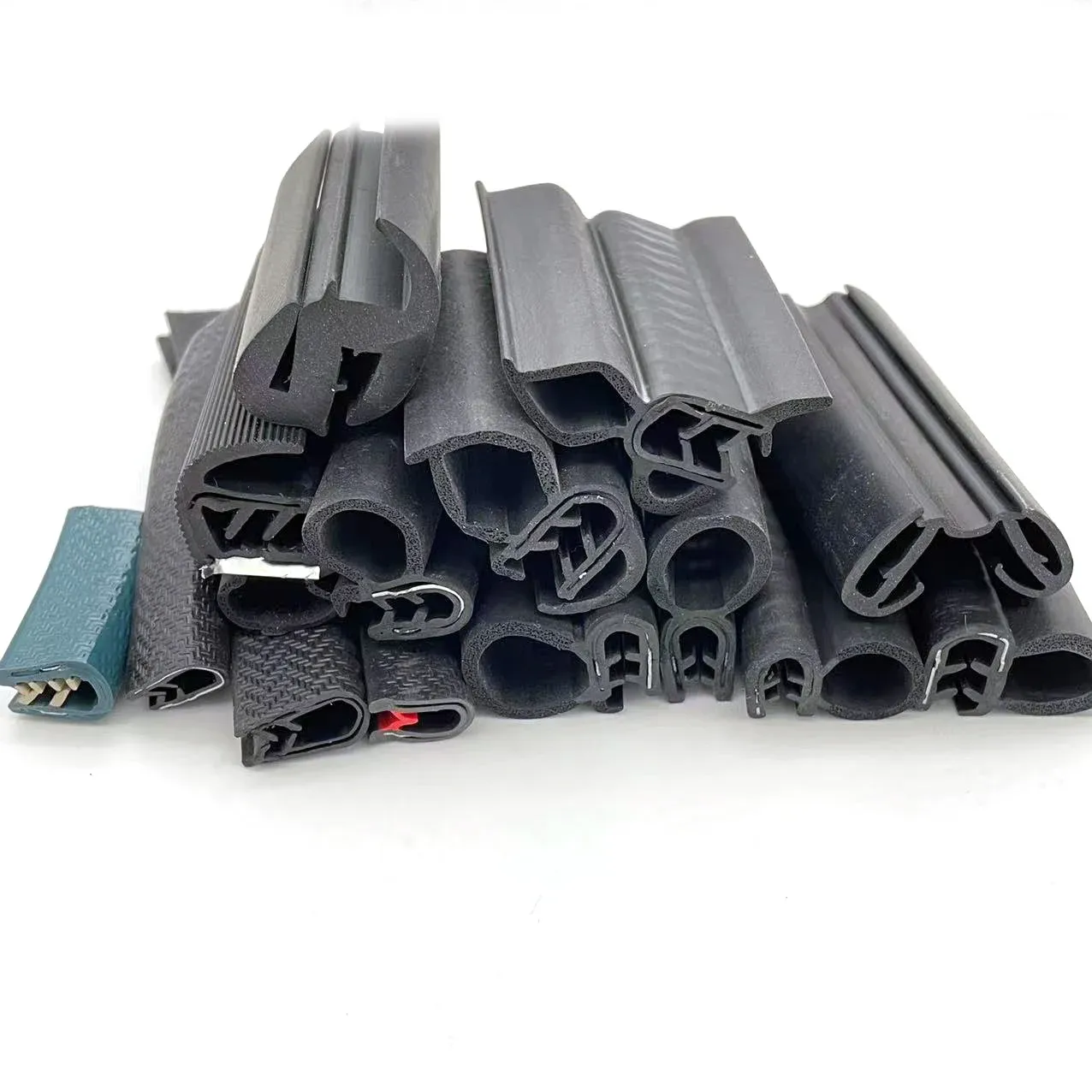
The flexibility and elasticity of silicone rubber seals also contribute to their widespread adoption. These seals maintain a reliable seal while accommodating slight imperfections and variations in component surfaces, which is essential for ensuring airtight and watertight seals. This adaptability not only enhances the longevity and reliability of the machines in which they are used but also reduces maintenance costs and downtime.
In the healthcare sector, silicone rubber seals are indispensable due to their biocompatibility. They are used extensively in medical devices and equipment where maintaining sterility and preventing contamination are paramount. Their non-reactive nature means they do not support microbial growth, making them ideal for applications that demand the highest level of hygiene and safety.
silicone rubber seals
From an engineering perspective, the manufacture of silicone rubber seals demands a high degree of expertise. The process typically involves the precise mixing of silicone polymers with various fillers and additives to attain desired characteristics. This tailoring of the material composition ensures compatibility with specific application requirements, such as enhanced tear strength or increased resistance to UV light.
Building trust with clients hinges on rigorous testing and quality assurance processes. Reputable manufacturers conduct extensive testing to ensure that silicone rubber seals meet or exceed industry standards. Such testing often includes exposure to extreme conditions to simulate real-world application scenarios, thereby verifying performance and reliability under duress.
Expertise in the design and application of silicone rubber seals also plays a critical role in their effectiveness. Engineers and designers must have an in-depth understanding of the material properties, as well as the demands of the application environment, to select or create seals that will perform optimally.
In conclusion, silicone rubber seals are a cornerstone in various industries, thanks to their exceptional temperature resilience, chemical resistance, flexibility, and biocompatibility. Their reliable performance not only enhances the efficiency and lifespan of industrial equipment but also underscores the technical expertise and innovation inherent in their design and application. For businesses seeking to aim for excellence in product integrity and reliability, incorporating high-quality silicone rubber seals is both a prudent and strategic decision.