Small rubber seals play a crucial role in various industries, serving as essential components that ensure the longevity and efficiency of machinery and devices. These unobtrusive yet vital parts are engineered to provide airtight and watertight seals in equipment ranging from automotive engines to industrial machinery. Their importance cannot be overstated as they help prevent leaks, maintain pressure, and safeguard against contamination.
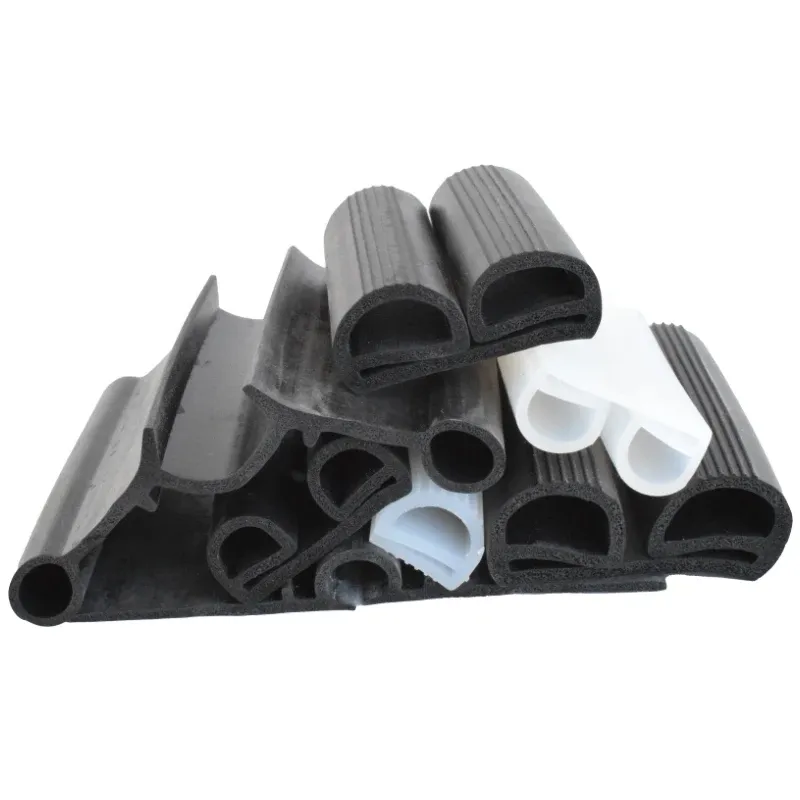
Drawing from decades of industry knowledge, it is clear that the demand for small rubber seals stems from their versatility and reliability. These seals are often crafted from synthetic rubber materials like EPDM, silicone, and nitrile, each offering unique properties suited to different applications. For instance, EPDM rubber is highly resistant to weathering and ozone, making it ideal for outdoor applications. Silicone rubber, known for its excellent temperature resilience, is frequently used in environments experiencing extreme temperatures. This adaptability across a range of conditions underscores their role in enhancing product performance.
From a technical viewpoint, small rubber seals are meticulously designed to meet specific performance criteria. Engineers rely on critical dimensions such as durometer hardness, tensile strength, and elongation at break to specify seals that will perform optimally within designated environments. Precise manufacturing processes and quality control measures are vital to producing seals that consistently meet these stringent specifications. Companies producing high-quality small rubber seals often employ advanced technologies such as computer-aided design (CAD) and finite element analysis (FEA) to simulate real-world conditions and iteratively refine their products.
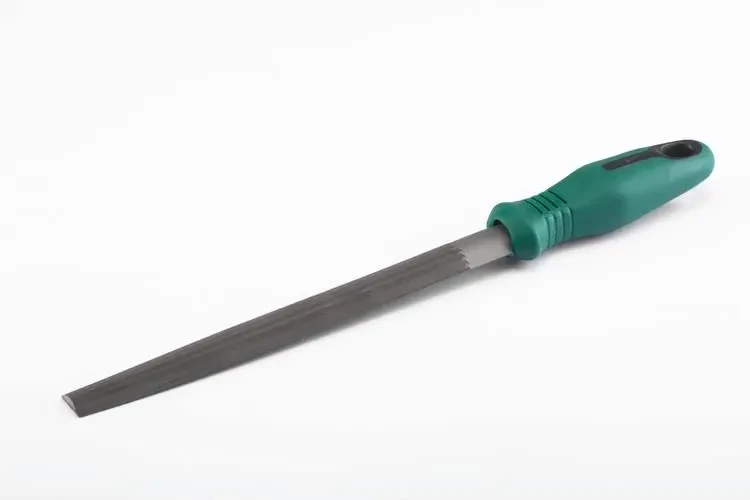
One noteworthy application of small rubber seals can be found in the automotive sector. Here, they serve in a variety of roles, from preventing fluid leaks in engines and transmissions to maintaining optimal air pressure in fuel systems. The reliability of these seals directly correlates with vehicle performance and safety, making their quality and durability paramount. As vehicles transition to electric models, the requirement for efficient sealing solutions becomes even more pronounced, with rubber seals playing a pivotal role in protecting sensitive electronic components from dust, moisture, and other environmental factors.
small rubber seals
The integrity of small rubber seals can make or break the operation of sophisticated systems, such as medical devices where sterility and precision are non-negotiable. In medical applications, seals must adhere to stringent standards for biocompatibility and cleanliness. Their ability to uphold these standards while maintaining flexibility and resilience is why they remain indispensable in the medical field.
Selecting the appropriate small rubber seal for a specific application is a decisive factor in the success of any project. Engineers and project managers often collaborate closely with experienced suppliers who provide not only products but consultative advice to ensure the right seal is selected. The reputation and credibility of the supplier play a significant role in this process, as businesses need assurance that the components they receive will meet regulatory and performance standards.
In a world where sustainability and ecological impact are becoming significant considerations, manufacturers of small rubber seals are innovating to produce more environmentally friendly products. By utilizing recyclable materials and optimizing production processes to reduce waste, the industry is gradually shifting towards more sustainable practices. Companies that actively embrace these changes position themselves as leaders in the market, combining product effectiveness with responsible stewardship of natural resources.
In conclusion, the essential nature of small rubber seals across numerous industries underlines the need for quality, reliability, and innovation in their design and production. As technology continues to evolve, the demand for sophisticated sealing solutions will only grow. By understanding the specific requirements and challenges of each application, manufacturers and engineers can ensure that these small components make a big difference.