The lithium-ion battery assembly line is a cornerstone of modern manufacturing, offering unmatched efficiency, precision, and scalability in the production of these vital energy storage devices. As the demand for electric vehicles (EVs), portable electronics, and renewable energy storage solutions increases, the significance of optimizing battery assembly lines cannot be overstated. Understanding the nuances of this process not only highlights its complexity but also underscores its importance in the global shift toward sustainable energy solutions.

To achieve a seamless lithium-ion battery assembly operation, manufacturers must consider several critical phases. The first involves the preparation of electrodes, a step that combines art and science. All components, including cathodes and anodes, require precise coating with active materials like lithium cobalt oxide or graphite. This process demands a controlled environment to ensure the materials' performance and longevity. Implementing advanced coating techniques, such as slot-die or extrusion coating, can significantly improve the uniformity and adherence of materials, ultimately enhancing battery efficiency.
Following electrode preparation, the next stage is cell stacking or winding. The decision between these methods depends on the intended application of the batteries. Stacking typically suits prismatic cells, while winding is preferred for cylindrical and pouch cells due to its capacity to create compact and uniform layers. Utilizing high-precision automation technology during this stage reduces the risk of misalignment, which can compromise electrical performance and safety.
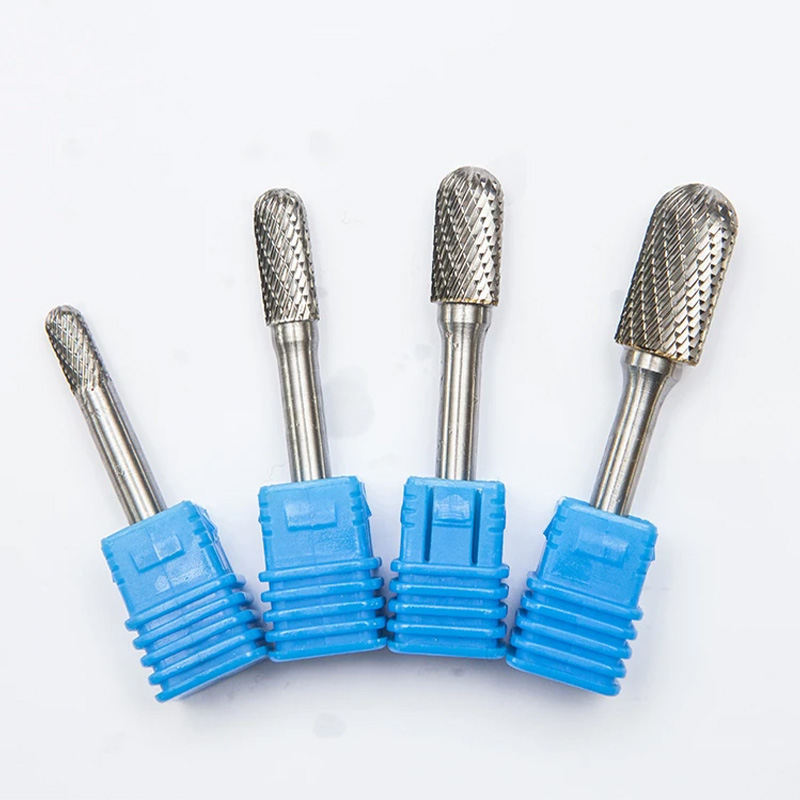
Once the cell is formed, it undergoes electrolyte filling and sealing—a step demanding extraordinary attention to detail. The electrolyte acts as a medium for ion transfer, and any contamination during filling can drastically undermine battery life and safety. Advanced filling technologies that minimize exposure to air and humidity can mitigate these risks, ensuring each cell's integrity. Following this, the stringent sealing process uses laser welding or ultrasonic methods to perfectly encapsulate the cell, preventing leaks and safeguarding against external pollutants.
Pre-production testing forms another pillar of a successful lithium-ion battery assembly line. Integrating automated testing systems, capable of real-time data analysis, enables the identification of defects or performance issues at early stages. This proactive approach enhances overall quality and reduces waste, aligning with efficient production practices. Testing parameters like capacity, internal resistance, and voltage efficiency are crucial metrics that assure the reliability of the batteries before they reach the consumer.
lithium ion battery assembly line
Committed to sustainable and high-quality production, the incorporation of Industry 4.
0 technologies is reshaping lithium-ion battery assembly lines. By utilizing Internet of Things (IoT) devices, artificial intelligence (AI), and big data analytics, manufacturers can monitor and optimize every aspect of the assembly process. Predictive maintenance tools, powered by AI, forecast machine downtimes and reduce unexpected stops, effectively eliminating production bottlenecks and improving output consistency.
In addition to technology, rigorous supply chain management is paramount. Sourcing raw materials such as lithium and cobalt ethically not only meets regulatory requirements but also enhances the company's reputation and consumer trust. Establishing partnerships with responsible suppliers ensures that the components used are of the highest quality, reflecting the company's commitment to sustainable practices and corporate responsibility.
Finally, workforce training and development cannot be ignored. Skilled personnel are vital in maintaining the high standards required in lithium-ion battery assembly. Regular training sessions and workshops keep staff updated with the latest technological advancements and best practices. This not only boosts operational efficiency but also fosters an environment of innovation and continuous improvement.
In conclusion, the optimization of lithium-ion battery assembly lines requires a holistic approach encompassing cutting-edge technology, meticulous quality control, ethical sourcing, and skilled human resources. As the world increasingly pivots towards electrification, efficient and sustainable battery production will play a pivotal role in powering the future. Manufacturers who invest in such comprehensive strategies are positioning themselves not only as leaders in the industry but as pioneers of the green energy revolution.