Custom molded rubber seals stand as unsung heroes in a wide array of industries, consistently delivering reliability and performance across diverse applications. While these components may appear discreet, their importance in machinery, automotive, aerospace, and consumer electronics is unquestionable. Understanding the expertise and trustworthiness involved in manufacturing these seals is crucial for any business looking to achieve optimal performance and longevity in its products.
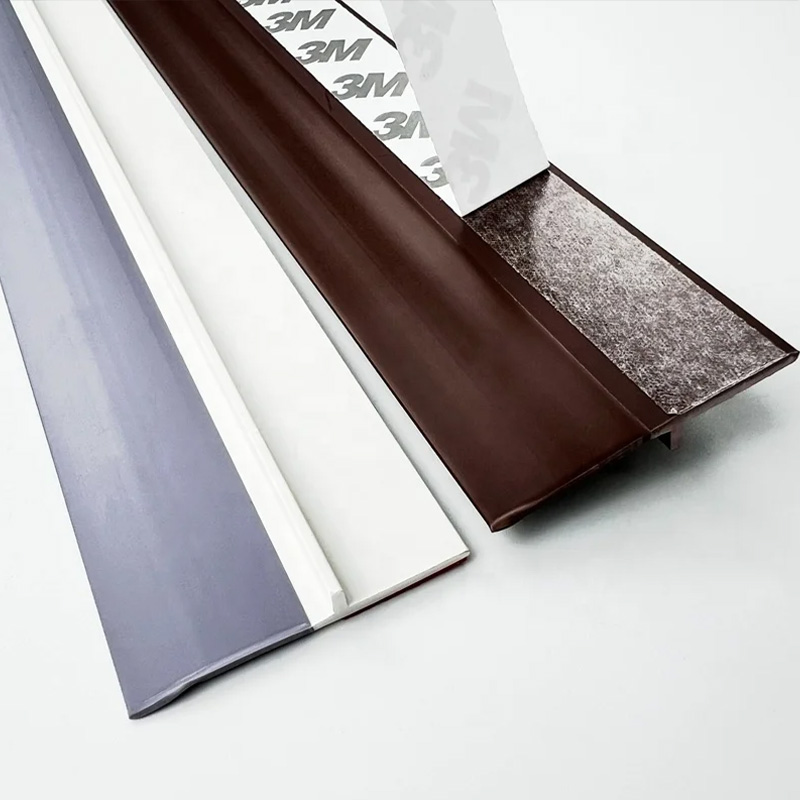
In the realm of manufacturing, the experience and proficiency involved in creating custom molded rubber seals cannot be overstated. Tailoring these seals requires a deep understanding of material properties, specific use cases, and environmental challenges. High-quality seals are not just about preventing leaks; they ensure that systems operate smoothly under extreme conditions. The process begins with selecting the appropriate elastomer – ranging from nitrile, silicone, EPDM, to fluorocarbon – each offering distinct advantages in terms of temperature resistance, chemical compatibility, and mechanical strength.
The manufacturing process itself is an intricate dance of precision engineering. Expert engineers use computer-aided design (CAD) tools to create detailed specifications, taking into account the seal’s dimensional tolerances and potential deformation under stress.
This is followed by mold design, where the craftsmanship truly becomes art. The mold is developed to exact standards to ensure that each seal is produced uniformly without defects. Precision in this stage guarantees that every custom molded seal fits perfectly into its designated assembly, providing unmatched reliability.
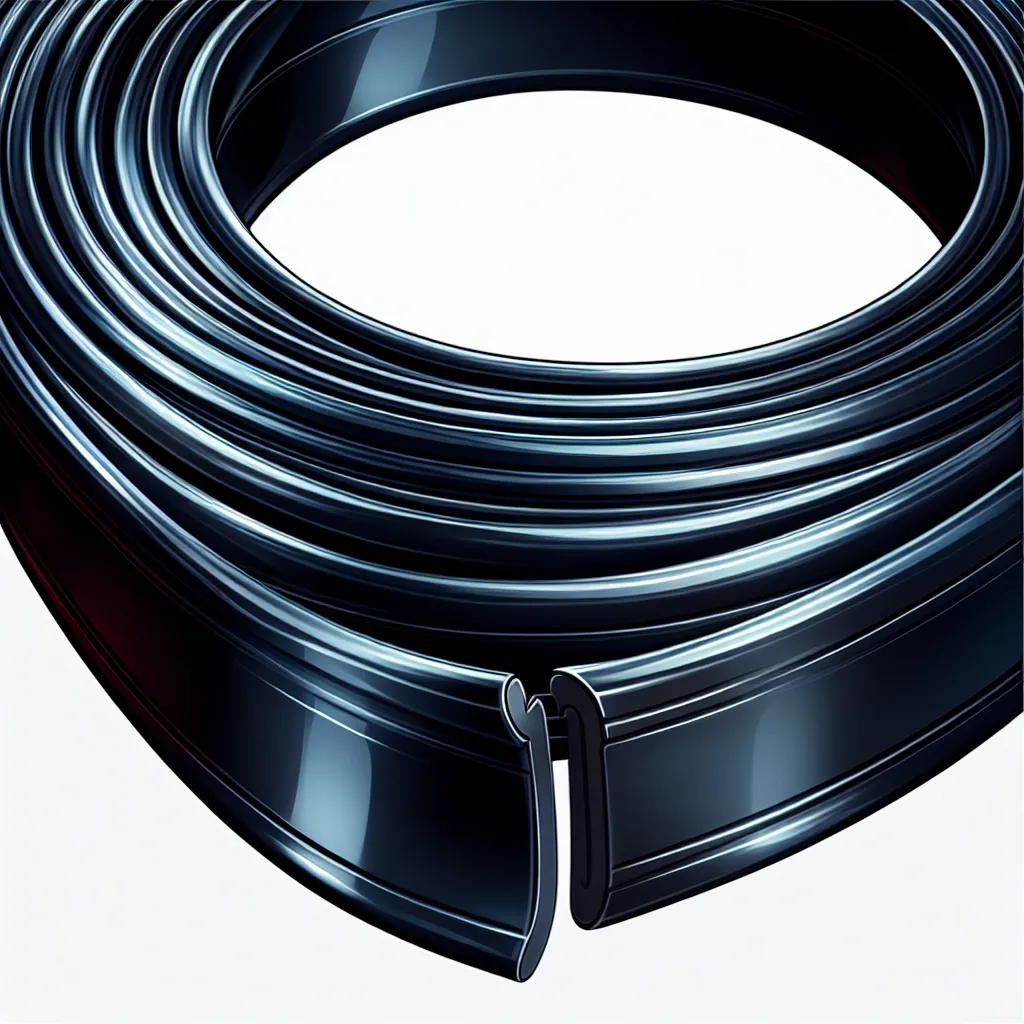
Quality control in producing rubber seals exemplifies authoritativeness within the manufacturing sector. Reputable manufacturers subject their seals to rigorous testing, simulating real-world application environments. This includes thermal cycling tests to gauge how the seals perform under fluctuating temperatures, and compression set tests to determine their ability to retain elasticity over prolonged periods. Such evaluations are conducted under strict adherence to international quality standards like ISO 9001 and IATF 16949, ensuring that each product meets global requirements for performance and safety.
custom molded rubber seals
In industries where downtime equates to significant financial loss, the trustworthiness of custom molded rubber seals becomes paramount. Seals that fail prematurely can lead to costly repairs and operational hiccups. Organizations, therefore, prioritize partnerships with manufacturers that demonstrate a proven track record of reliability and customer satisfaction. This trust is built over years, through consistent delivery of products that not only meet but often exceed industry expectations.
Further cementing their authority, leading manufacturers often engage directly with clients during the seal development process. They offer consultancy services to help businesses optimize seal designs for specific applications, considering factors such as pressure, temperature extremes, and exposure to chemicals. By doing so, they leverage their extensive knowledge and experience to provide solutions that are both practical and tailored.
Moreover, advances in material science have empowered manufacturers to create more innovative solutions. For example, the development of seals with enhanced attributes such as self-lubricating surfaces or anti-static properties showcases the sector's commitment to continuous improvement and adaptability. These innovations not only expand the functional possibilities of rubber seals but also enhance performance in challenging environments, providing a competitive advantage to the end users.
In conclusion, custom molded rubber seals are indispensable components, backdrop heroes essential for the functionality and durability of thousands of products we rely on daily. Their manufacture is a testament to the blend of experience, expertise, authority, and trust upon which industries build their successes. For businesses seeking to incorporate high-quality rubber seals, aligning with knowledgeable and reliable manufacturers is not just beneficial—it is essential for competitive and operational excellence.