The Essential Role of Molded Rubber Seals in Industrial Applications
Molded rubber seals have become an integral component in various industries, from automotive and aerospace to construction and electronics. These versatile rubber products are designed to provide a reliable barrier against fluid leakage, dust ingress, and other forms of contamination, ensuring the smooth operation and longevity of machinery and equipment. As such, finding a reputable molded rubber seals supplier is crucial for maintaining the efficiency and safety of industrial processes.
The manufacturing of molded rubber seals requires precise engineering to meet the specific demands of each application. A high-quality supplier will offer a wide range of materials, including EPDM (Ethylene Propylene Diene Monomer), silicone, viton, and neoprene, each with unique properties suited to different environments and pressures. For instance, oil-resistant viton is ideal for high-temperature automotive applications, while EPDM's durability makes it suitable for outdoor sealing in construction.
Furthermore, a competent supplier will possess advanced production techniques capable of creating complex geometries and custom designs. This capability ensures that seals can be tailored to fit precisely within various assembly configurations, enhancing performance and reducing the risk of failure.
Quality control is another hallmark of a top-tier supplier. Rigorous testing protocols should be in place to guarantee that each batch of seals meets industry standards for compression set, hardness, and elongation Rigorous testing protocols should be in place to guarantee that each batch of seals meets industry standards for compression set, hardness, and elongation
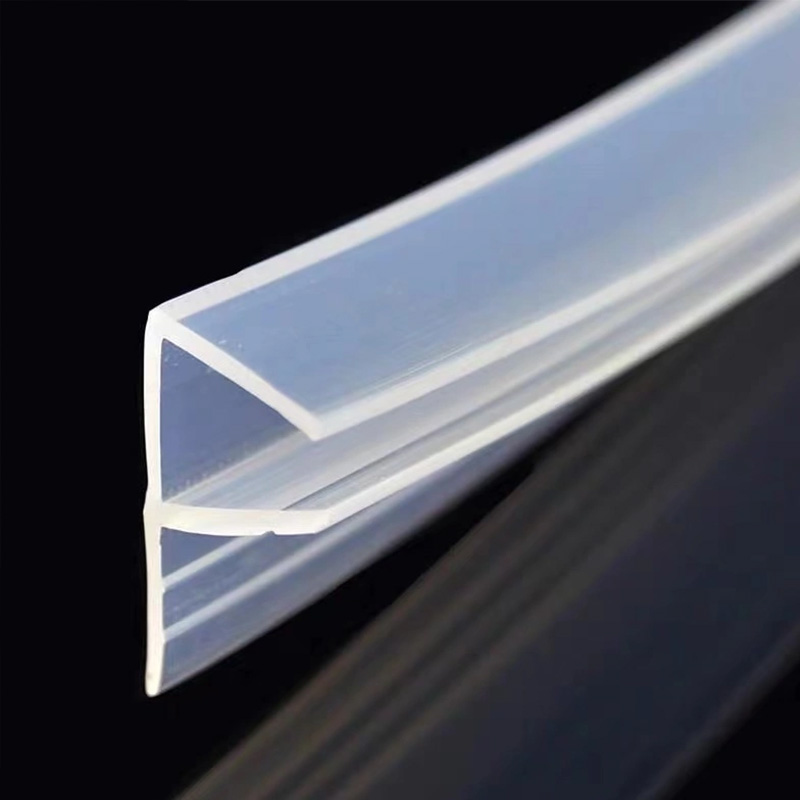
Rigorous testing protocols should be in place to guarantee that each batch of seals meets industry standards for compression set, hardness, and elongation Rigorous testing protocols should be in place to guarantee that each batch of seals meets industry standards for compression set, hardness, and elongation
molded rubber seals supplier. This attention to detail prevents field failures that could lead to costly repairs or downtime.
Suppliers who prioritize research and development often stay ahead of industry trends by offering innovative solutions. They may introduce new materials or improved designs that offer enhanced resistance to chemicals, extreme temperatures, or wear and tear. Their expertise can also guide customers in selecting the right seal for their specific needs, providing invaluable technical support.
Reliable supply chains and timely delivery are also critical factors when choosing a supplier. Inventory management systems should ensure that popular items are readily available, while custom orders can be quickly turned around without sacrificing quality.
In conclusion, selecting the right molded rubber seals supplier is vital to the success of any industrial operation that relies on these essential components. With meticulous craftsmanship, a broad material selection, stringent quality assurance, and responsive customer service, a superior supplier becomes a partner in maintaining the integrity of critical systems and paving the way for innovation and reliability across diverse sectors.