The prismatic cell manufacturing industry is a pivotal player in the modern energy landscape, driving advancements in battery technology essential for a future powered by renewable resources. The equipment used in the manufacturing of prismatic battery cells is a cornerstone for ensuring efficiency, quality, and scalability in production, making it crucial for manufacturers to understand and invest in state-of-the-art machinery.
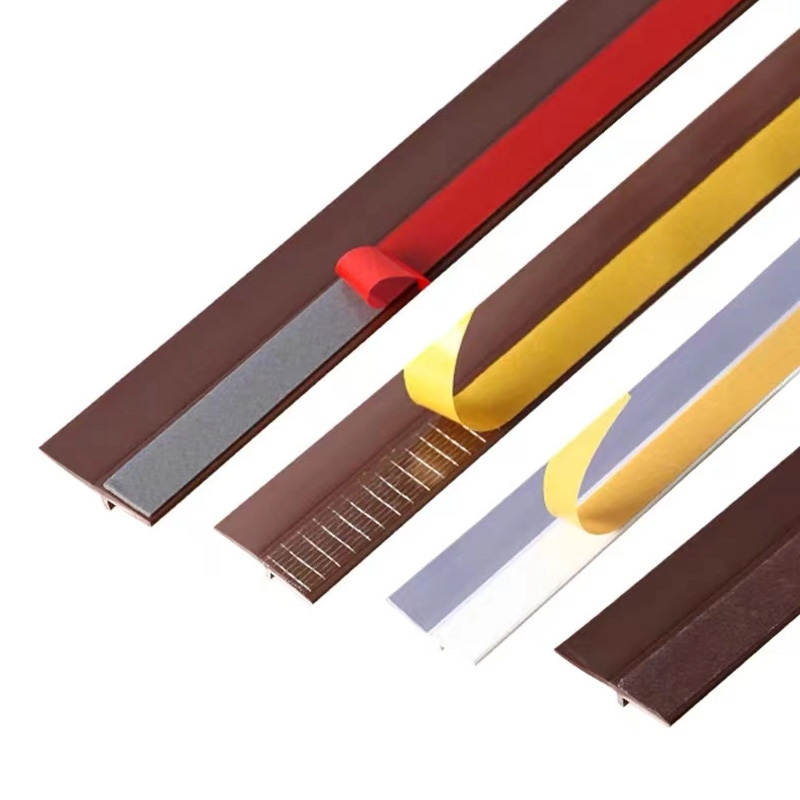
Experience shows that manufacturing equipment specifically designed for prismatic cells can significantly impact the performance and durability of the batteries produced. For instance, precision engineering in the cutting and folding machines ensures that the metallic foils used in the cells are manipulated without causing micro-tears that could lead to internal short circuits. Such meticulous attention to detail in the production process not only enhances the longevity of the cells but also their safety—a critical factor as industries continue to adopt lithium-based battery technologies.
Expertise in this sector is often marked by an in-depth understanding of the integration between the equipment and the materials used. The precision with which machinery can facilitate the layering of electrodes and separators within a prismatic cell directly affects the energy density and thermal management of the battery. As manufacturers aim to reduce costs while maximizing output, automated solutions are increasingly favored. Automated systems offer consistent, reliable operation, drastically minimizing human error and increasing throughput.
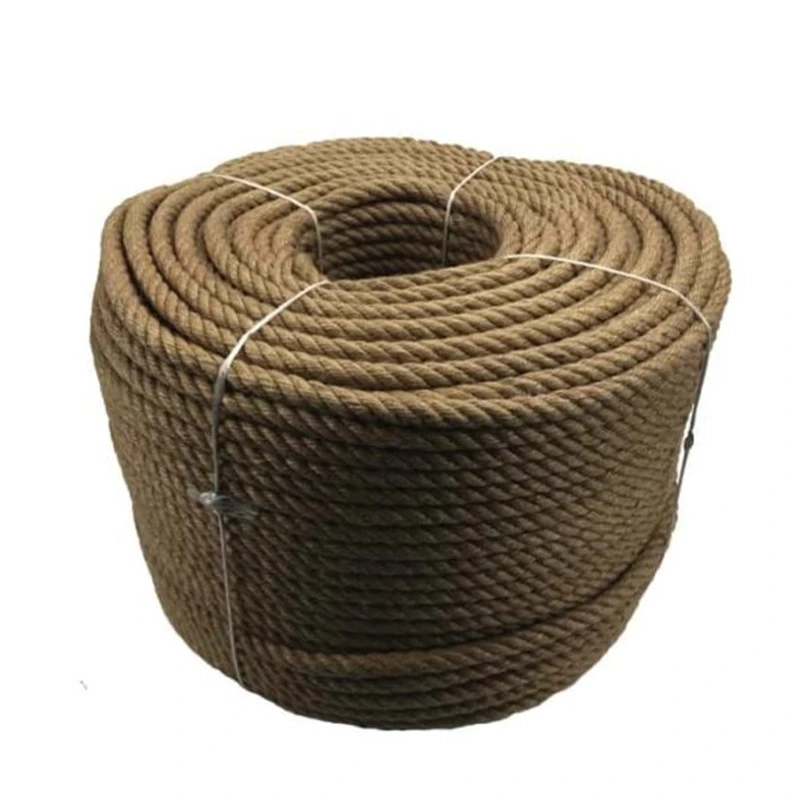
In terms of authoritativeness, industry standards and compliance are non-negotiable benchmarks that manufacturing equipment must meet. The International Electrotechnical Commission (IEC) and other regulatory bodies maintain strict guidelines on safety and efficiency, which equipment manufacturers need to adhere to. This is not only to ensure the safety of the end-users but also to maintain a competitive edge in a rapidly advancing market. As a recognized leader in this space, high-quality equipment manufacturers often collaborate with regulatory bodies to both meet and shape stringent safety and performance standards.
Trustworthiness is perhaps the most intangible yet critical feature of prismatic cell manufacturing equipment. The best practices in the industry emphasize transparency in supply chains and rigorous testing protocols to deliver products that can withstand the demands of varied applications, from electric vehicles to consumer electronics. Manufacturers that prioritize quality assurance, backed by extensive research and development, reassure stakeholders and consumers alike of the reliability of their products.
prismatic cell manufacturing equipment
In the quest to enhance production efficiency, modern prismatic cell manufacturing equipment incorporates advanced technologies like IoT and AI for monitoring and optimization. Real-time monitoring systems offer valuable insights into machine performance and maintenance needs, significantly reducing downtime. AI algorithms can predict potential failures and optimize operational parameters to ensure every produced cell meets the most exacting standards.
Furthermore,
sustainable manufacturing processes are now an integral part of equipment design. Energy-efficient machinery and waste reduction techniques not only align with environmental goals but also improve operational costs. Equipment that integrates recycling and repurposing of materials within the production line can reduce ecological impact, a growing concern for stakeholders and consumers alike.
To stay competitive, manufacturers must continually invest in training and development for their workforce to operate these sophisticated machines. This commitment to workforce development ensures that operators are well-versed in the latest technological advancements and safety protocols, maintaining the integrity and efficiency of their production lines.
In summary, the right prismatic cell manufacturing equipment is a vital investment for any company aiming to produce high-quality, reliable batteries. Leveraging experience, expertise, and the latest technology while adhering to authoritative standards and building trust through transparency and reliability can position manufacturers at the forefront of the battery revolution. As demand for efficient energy storage solutions grows, so too will the need for cutting-edge manufacturing solutions that can deliver on performance and sustainability, shaping the future of power as we know it.