Waterproof rubber seals play a crucial role in various industries, providing an essential barrier against moisture, dirt, and environmental contaminants. These components are integral in ensuring the longevity and reliability of products ranging from consumer electronics to automotive applications. Drawing from years of expertise in material sciences and practical applications, this article delves into the intricacies and benefits of waterproof rubber seals.
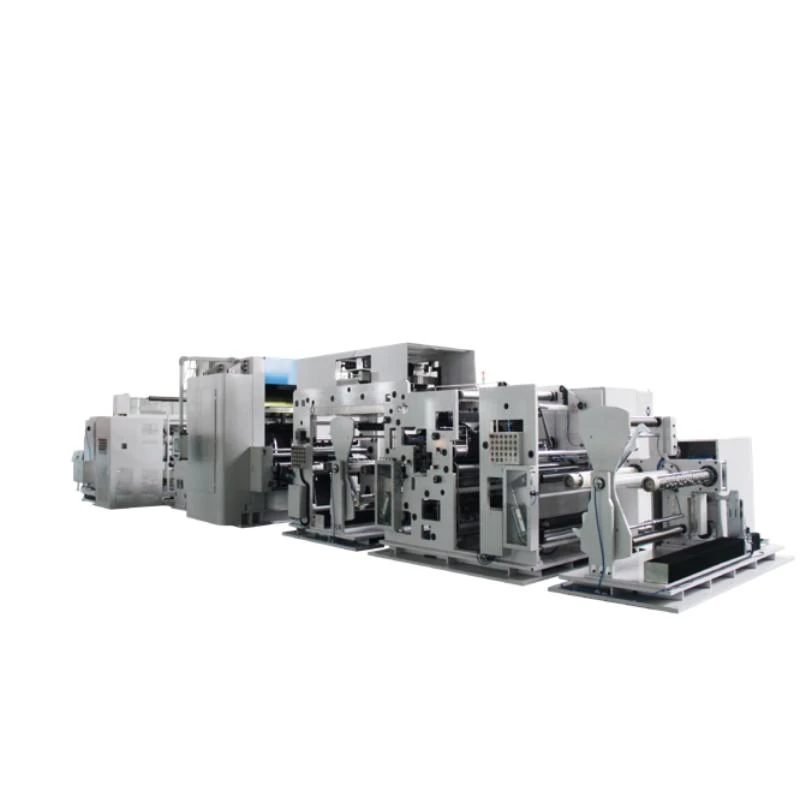
In the realm of engineering and design, the functionality of a product can significantly depend on the integrity of its seals. Waterproof rubber seals are crafted from high-performance elastomers that not only resist water but also maintain elasticity and resilience over a wide range of temperatures and pressures. Common materials used include silicone, EPDM (ethylene propylene diene monomer), and nitrile rubber, each offering unique properties that suit different applications.
Silicone rubber seals are renowned for their flexibility and can withstand both extreme cold and heat, making them ideal for use in environments that experience significant temperature fluctuations. These characteristics make silicone seals a top choice in the medical, food, and beverage industries where sterilization and consistent performance are paramount. In contrast, EPDM seals provide excellent resistance to UV rays, ozone, and weather, which is why they are frequently used in outdoor applications, including in the automotive and construction sectors.
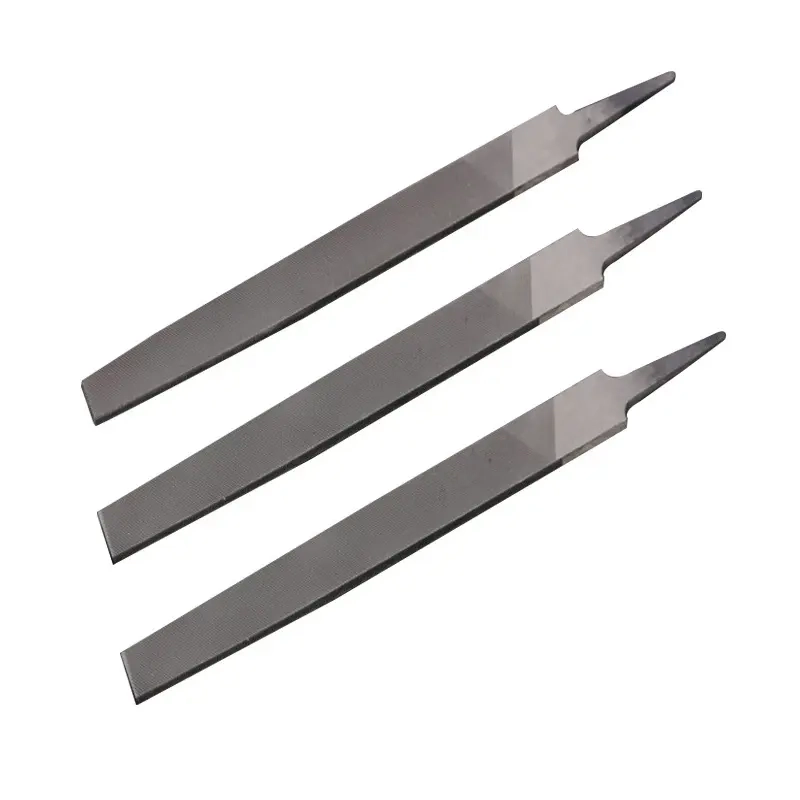
In automotive applications, waterproof rubber seals are indispensable. They are utilized around doors, windows, trunks, and hoods to prevent leaks that could lead to rust formation and electrical system failures. Their role in maintaining vehicle integrity under various environmental conditions underscores their importance in the automotive sector. Not only do they prevent water ingress, but they also dampen noise and absorb vibrations, enhancing overall driving comfort.
When selecting waterproof rubber seals, it's important to consider the specific application requirements. This involves analyzing the environmental factors, such as exposure to chemicals, temperature range, and mechanical stresses involved. For industries that deal with chemical exposure, nitrile rubber seals offer excellent resistance to oils and other hazardous substances. They are commonly used in industrial machinery and fuel systems where they can provide reliable sealing solutions without degrading.
waterproof rubber seals
The longevity and effectiveness of waterproof rubber seals also hinge on proper installation and maintenance. Ensuring the seals are correctly fitted into their designated grooves or channels is crucial in maintaining a seamless barrier against moisture and pollutants. Routine inspections and timely replacements of worn-out seals will prevent potential failures, safeguarding the integrity of the overall system or product.
Innovation in the field of waterproof seals is ongoing, with new materials and designs being developed to meet the ever-increasing demands of modern applications. Advanced sealing technologies are being implemented to increase durability and efficiency, such as specialized coatings that enhance the material's resistance to extreme environments and reduce friction during compression and decompression cycles.
Furthermore,
the rise of sustainable materials in manufacturing is impacting the development of eco-friendly rubber seals. Researchers and manufacturers are looking into bio-based elastomers and recycling processes to minimize environmental footprints. This shift not only supports sustainability goals but also opens up new avenues for product development in industries that prioritize environmental stewardship.
The importance of waterproof rubber seals cannot be overstated, as they are fundamental to ensuring the longevity and reliability of numerous products and systems. Their application across different industries showcases their versatility and the necessity for high-quality seals. Industry specialists advocate for thorough testing and adherence to stringent industry standards to maximize the efficacy and durability of seals, underscoring the importance of trustworthiness and authority in their production.
As technology evolves, waterproof rubber seals will continue to be at the forefront of innovative solutions tailored to meet the changing needs of industrial and consumer applications. The harmonious blend of material science advancements and practical expertise ensures that waterproof seals will provide dependable performance, securing their place as an essential component in various sectors for years to come.