The Art of Precision Rasp Technology in Modern Woodworking Factories
In the realm of woodworking craftsmanship, a process that has stood the test of time and continues to evolve is rasping. The term rasp to make wood flat refers to the use of rasp tools in factories to refine and level surfaces with remarkable precision. This technique, an integral part of woodworking lore, has transformed from manual labor to high-tech automation, revolutionizing the industry.
Raping, once a labor-intensive task, involved using hand-held rasps, often made of steel or other durable materials, to gradually smooth and flatten rough or uneven wood surfaces. Workers would painstakingly rub the rasp against the wood, removing thin layers until the desired flatness was achieved. However, as technology advanced, so did the efficiency and accuracy of this process.
Modern woodworking factories now employ state-of-the-art power rasp machines, equipped with computer-controlled mechanisms. These devices utilize abrasive belts or disks that rotate at high speeds, allowing for faster and more consistent flattening. The rasp-to-make-wood-flat factories have incorporated sophisticated software that can program the machine's movement, ensuring minimal waste and optimal surface finish.
These machines not only save time but also improve the overall quality of the final product. They can work on larger pieces with uniformity, making it possible to achieve a level of precision that was once impossible by hand. Additionally, they reduce operator fatigue and minimize the risk of human error, which can be detrimental to the integrity of the wood Additionally, they reduce operator fatigue and minimize the risk of human error, which can be detrimental to the integrity of the wood
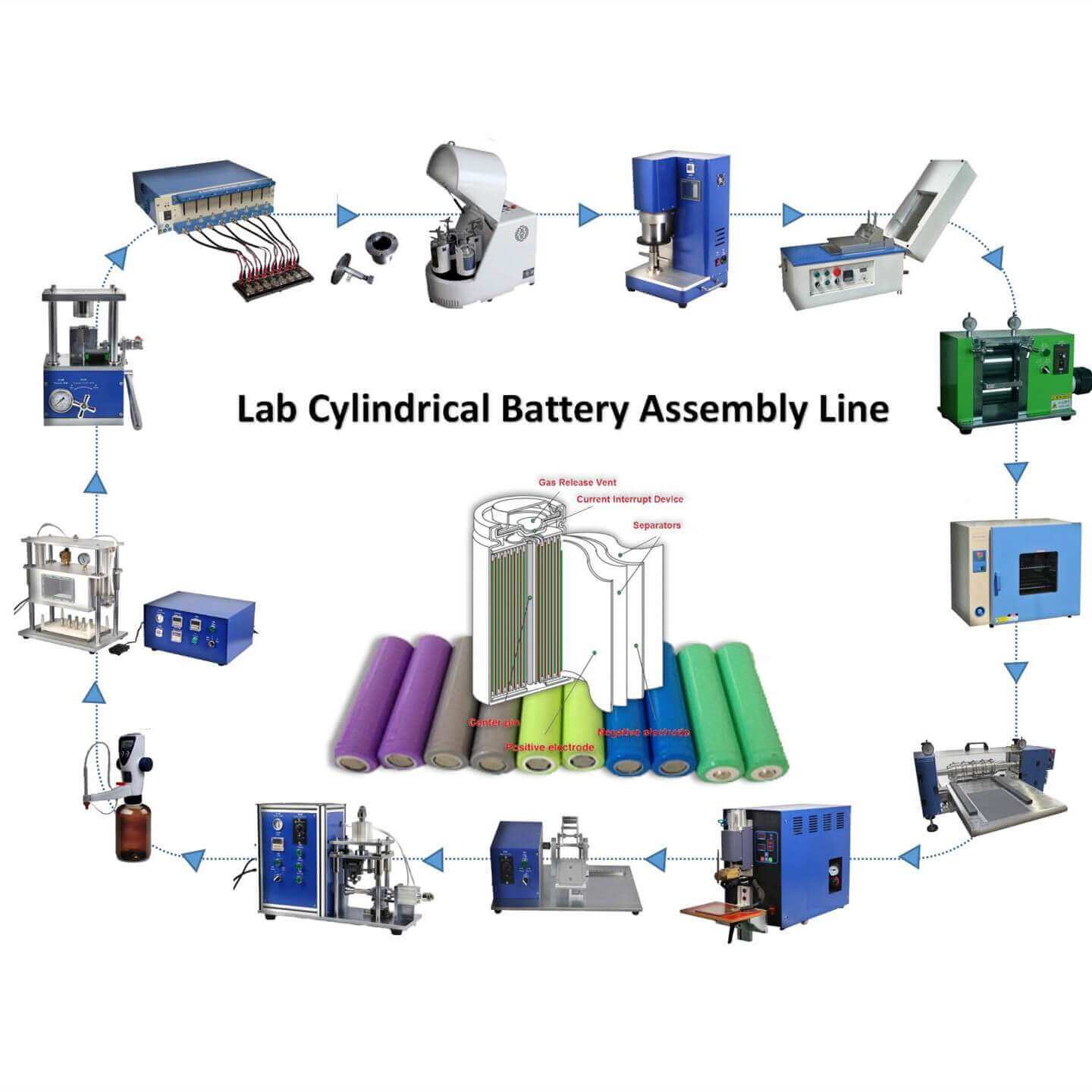
Additionally, they reduce operator fatigue and minimize the risk of human error, which can be detrimental to the integrity of the wood Additionally, they reduce operator fatigue and minimize the risk of human error, which can be detrimental to the integrity of the wood
rasp to make wood flat factory.
Furthermore, the integration of digital scanning technology has further enhanced the rasp process. By scanning the wood beforehand, manufacturers can create a digital blueprint, guiding the rasp machine to correct any irregularities with pinpoint accuracy. This step-by-step approach ensures that even the most complex shapes can be leveled flawlessly.
Despite the advancements in technology, the artistry and craftsmanship of woodworking remain essential. The rasp-to-make-wood-flat factories serve as a bridge between tradition and innovation, preserving the essence of woodworking while embracing the benefits of modern machinery. The result is a harmonious blend of human skill and technological prowess, pushing the boundaries of what is achievable in woodworking.
In conclusion, the evolution from traditional rasp methods to high-tech factories demonstrates the continuous adaptation of woodworking to meet the demands of a changing world. As we marvel at the precision and efficiency of these factories, let us not forget the rich history and human touch that lies at their core. The rasp-to-make-wood-flat process stands as a testament to the resilience and adaptability of both woodworking and the skilled artisans who master it.