The evolution of the automotive industry is intrinsically linked to the rapid advancements in electric vehicles (EVs), with a significant focus on the EV battery assembly line. This state-of-the-art technology is critical to the future of sustainable transportation, transforming how vehicles are powered and how efficiently they can operate.
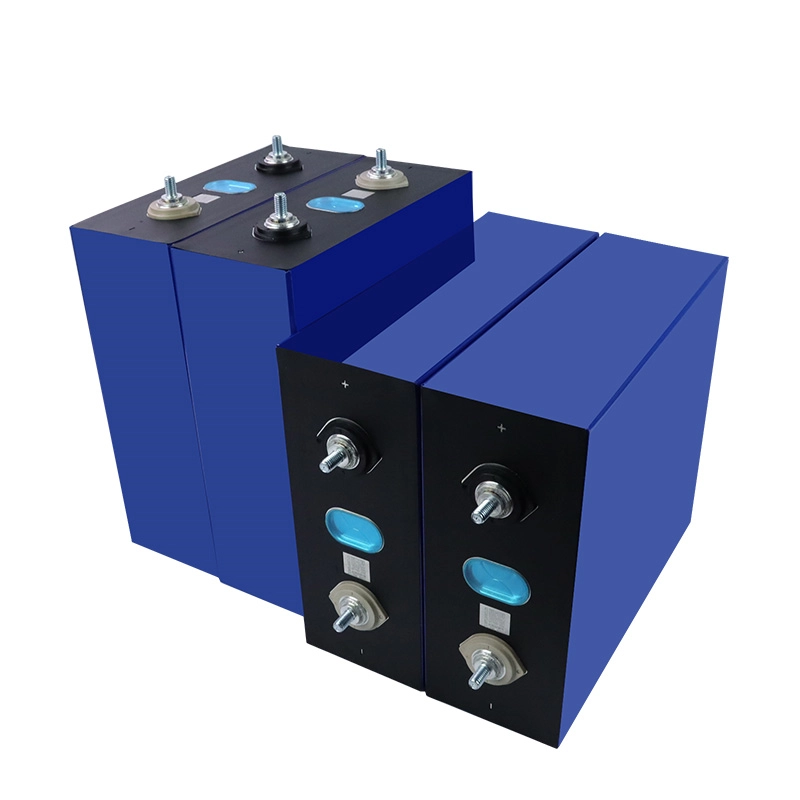
The assembly line for EV batteries is more than just a technological marvel; it is a crucial component that determines the efficiency, safety, and reliability of electric vehicles. Manufacturers invest heavily in refining this process, as it directly influences the overall performance and appeal of their EVs to consumers. A high-quality battery assembly line can drastically reduce production costs while enhancing battery life and energy efficiency.
Experience in this realm reveals that precision engineering is the backbone of any efficient EV battery assembly line. Ensuring that each cell within the battery is accurately placed and connected is paramount. This precision prevents energy loss and ensures uniform charging and discharging cycles, which are vital for maximizing the lifespan of the battery. Companies often employ automated guided vehicles and robotic arms to handle these tasks, minimizing human error and ensuring each battery pack is created under exacting specifications.
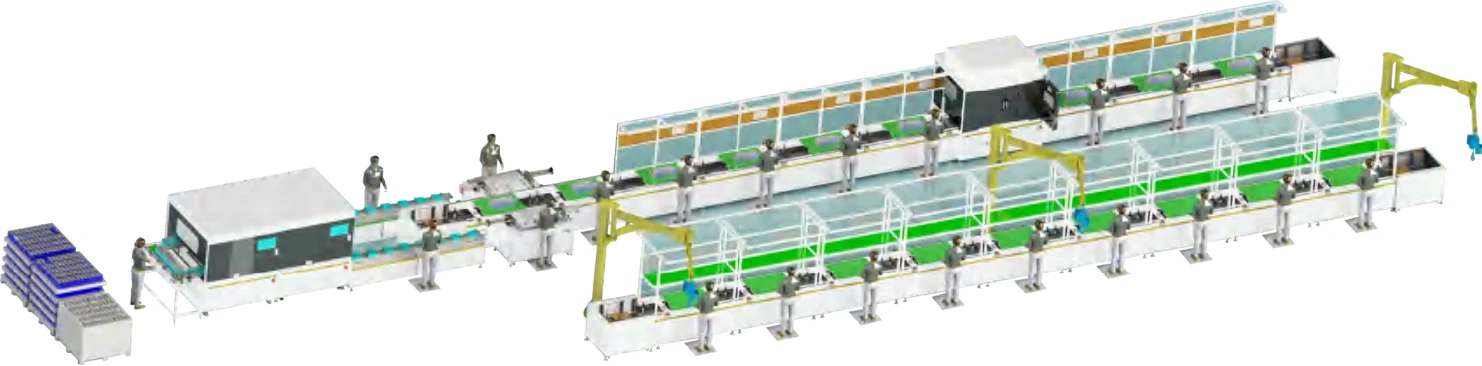
From an expertise perspective, understanding the chemistry behind battery cells is crucial. Lithium-ion remains the most prevalent technology due to its high energy density, but innovations are rapidly emerging. Solid-state batteries, for instance, offer promise with even greater energy capacity and safety features. As manufacturing techniques advance, staying abreast of these developments is essential for any entity within the EV battery production landscape.
ev battery assembly line
Analyzing authoritative insights reveals that compliance with international safety and environmental standards is non-negotiable. Organizations such as the International Electrotechnical Commission (IEC) and the Underwriters Laboratories (UL) set stringent guidelines that govern battery safety and performance. Adherence to these standards not only ensures product safety but also bolsters the manufacturer's reputation in the global market, a critical factor in an industry built on trust and reliability.
Trustworthiness in EV battery assembly involves a commitment to transparency and quality assurance. Manufacturers must maintain rigorous testing protocols to ascertain the reliability of their battery packs. Performance under various conditions, including temperature extremes and different charging scenarios, needs thorough evaluation. Customers today demand not only high performance but also assurances of durability and safety, and consistent test results are key to delivering that promise.
Lastly, real-world applications and customer feedback play indispensable roles in refining the assembly process. Frontline employees and engineers often provide crucial insights into potential bottlenecks in the production line or areas where efficiency could be improved. Collaborating with automotive manufacturers to receive feedback on battery performance in vehicles allows producers to make targeted improvements, ensuring that the assembly lines produce batteries that meet the practical needs and expectations of end-users.
As the automotive world continues its shift towards electrification, the role of EV battery assembly lines becomes ever more critical. They are the lifeline that powers the future of mobility, reducing our reliance on fossil fuels and paving the way for a cleaner, more sustainable environment. Therefore, staying at the cutting edge of technology, adhering to the highest standards of safety, and maintaining a customer-centric approach are integral for any business committed to excelling in the EV battery market. Building a reputable brand in this nascent yet rapidly expanding sector hinges on the experience, expertise, authoritativeness, and trustworthiness of its EV battery assembly operations.