Rubber seals for bearings are indispensable components across various industries, extending their influence far beyond what meets the eye. Experience and expertise in selecting the right rubber seal can significantly enhance the bearing's efficiency and longevity.
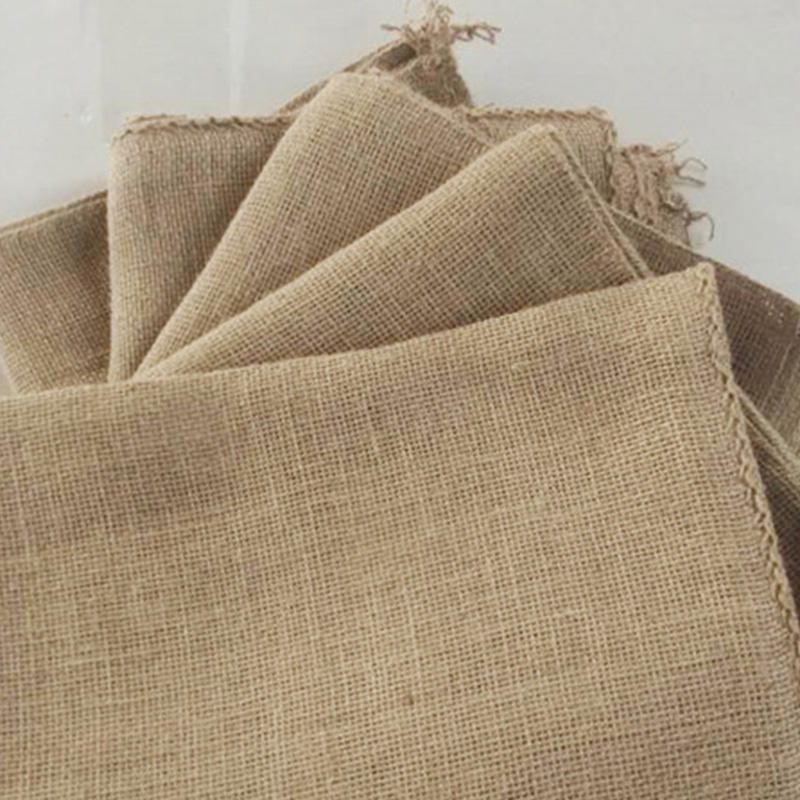
As industries strive to optimize their machinery and equipment, the demand for durable rubber seals escalates. These seals, crafted from high-quality elastomers, provide a protective barrier that safeguards the bearings against contaminants, reducing the risk of premature failure. Their effectiveness in maintaining performance under stringent conditions stands as a testament to their impeccable design.
The expertise in engineering and manufacturing rubber seals for bearings requires a deep understanding of their application environment. Engineers must consider factors such as temperature fluctuations, exposure to chemicals, and mechanical stress. The selection process involves analyzing the composition of the rubber materials—such as nitrile, silicone, or Viton—each offering unique properties suited for specific operational requirements. For instance, silicone seals exhibit exceptional heat resistance, making them ideal for high-temperature applications, while nitrile rubber offers excellent resistance to petroleum-based oils and fuels.
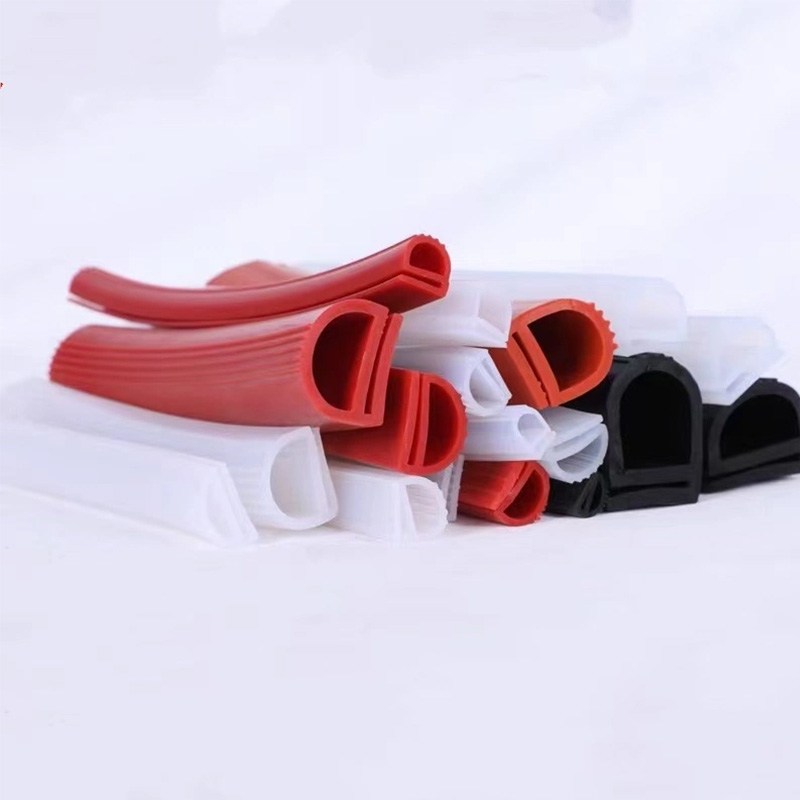
Establishing authoritativeness in the manufacturing of rubber seals demands a commitment to quality and innovation. Leading manufacturers employ state-of-the-art technologies to design seals that not only meet but exceed industrial standards. This includes rigorous testing for durability, flexibility, and resistance to wear and tear. Companies that excel in this domain often collaborate with research institutions to pioneer advancements in material science, ensuring their products remain at the forefront of technological innovation.
Trustworthiness is a keystone in the relationship between manufacturers and their clients. Transparency in the production processes, along with clear communication about the attributes and limitations of rubber seals, fosters a trust-based partnership. Providing comprehensive guides and support for installation and maintenance ensures clients derive maximum value from their investment, thereby enhancing the operational lifespan of their machinery.
rubber seals for bearings
The role of rubber seals extends into specialized areas such as aerospace, automotive, and industrial machinery—each presenting unique challenges that demand tailored solutions. In aerospace, for instance, rubber seals must withstand extreme altitudes and pressures, necessitating precision in engineering to eliminate any risk of malfunction. Similarly, automotive bearings endure high rotational speeds and variable environmental conditions, requiring seals that can adapt to these dynamic environments.
Harnessing the potential of rubber seals for bearings involves not just their application, but also understanding the science behind their development. The integration of advanced analytics and simulation technologies aids manufacturers in predicting seal performance and lifecycle, which in turn informs their design and material selection process.
Quality management systems, such as ISO certifications, further reinforce a manufacturer's commitment to excellence. Such endorsements reassure clients of the product's reliability, as compliance with international standards is indicative of consistent quality and safety measures.
In conclusion, the landscape of rubber seals for bearings is rich with opportunities for innovation and precision engineering. The blend of experience, expertise, authority, and trust instills confidence in these small yet mighty components. As industries evolve, the role of rubber seals will continue to be pivotal, driving efficiency and reliability across sectors worldwide. By staying at the cutting edge of technology and maintaining a client-centric approach, manufacturers can deliver products that not only solve immediate challenges but also anticipate future industry needs.