In the rapidly growing electric vehicle (EV) market, optimizing car battery production line, car battery assembly line, and umugqa wokuhlanganisa ibhethri ev is key for manufacturers to stay competitive. Xingtai Shuoding Trading Co., Ltd. offers a range of high - quality equipment that can significantly enhance the efficiency, quality, and cost - effectiveness of these assembly lines, presenting great opportunities for wholesalers looking to provide valuable solutions to their customers.
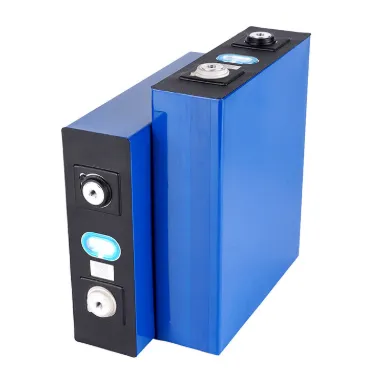
Enhancing Efficiency in EV Battery Assembly Line
- Automated Material Handling: Implementing automated systems in the EV battery assembly line is crucial for efficiency. Automated guided vehicles (AGVs) can transport battery components precisely and quickly between different workstations. This reduces the time wasted in manual material transfer and minimizes the risk of damage to sensitive battery parts. Additionally, robotic arms can be used for tasks such as cell picking and placing, ensuring consistent and rapid assembly operations.
-
- Process Sequencing Optimization:Carefully planning the sequence of operations in the EV battery assembly line can avoid bottlenecks. By analyzing the production process flow, manufacturers can determine the most efficient order of tasks, such as battery cell sorting, module assembly, and pack integration. This optimization ensures a smooth and continuous production flow, maximizing the output of the assembly line.
-
- Real - Time Monitoring and Control: Installing sensors and monitoring devices along the EV battery assembly lineenables real - time tracking of production parameters. Data on production speed, quality metrics, and equipment status can be collected and analyzed. Based on this information, adjustments can be made promptly to optimize the performance of the assembly line, ensuring that it operates at peak efficiency at all times.
Improving Quality in Car Battery Assembly Line
- Precision Component Alignment: In the car battery assembly line, precise alignment of battery components is essential for quality. Advanced positioning systems can be used to ensure that battery cells, connectors, and other parts are placed accurately. This precision reduces the risk of electrical shorts, poor connections, and other issues that could affect battery performance and safety.
-
- Stringent Quality Inspection: Incorporating multiple quality inspection points in the car battery assembly linehelps catch defects early. Automated optical inspection (AOI) systems can detect visual flaws, while electrical testing equipment can verify the functionality of battery modules and packs. By performing thorough inspections at various stages, manufacturers can ensure that only high - quality products leave the assembly line.
- Traceability Systems: Establishing traceability systems in the car battery assembly lineallows for easy identification of the origin of components and the production history of each battery. This is important for quality control, as it enables manufacturers to quickly address any quality issues by tracing back to the specific production batch or component supplier.
Innovation in Car Battery Production Line
- Advanced Manufacturing Technologies: Adopting cutting - edge manufacturing technologies in the car battery production linecan revolutionize the production process. For example, 3D printing can be used to produce custom battery components or prototypes quickly, reducing development time and costs. Additionally, laser welding technology can provide stronger and more reliable connections in battery assembly, improving the overall durability of the batteries.
- Digital Twin Integration:Creating a digital twin of the car battery production line allows for virtual simulation and optimization. Manufacturers can test different production scenarios, process improvements, and equipment configurations in the digital environment before implementing them in the actual production line. This reduces the risk of disruptions and enables more informed decision - making for continuous improvement.
- Sustainable Production Practices: Incorporating sustainable production practices in the car battery production lineis not only environmentally friendly but also cost - effective. Recycling and reusing materials, optimizing energy consumption, and reducing waste generation can all contribute to a more sustainable and efficient production process. Xingtai Shuoding Trading Co., Ltd.'s equipment can be designed to support these sustainable initiatives.
Product Specifications of Xingtai Shuoding Trading Co., Ltd.'s Assembly Line Equipment
Parameter
|
Imininingwane
|
Inombolo Yemodeli
|
SD - EV30
|
Compliance
|
I-CE iqinisekisiwe
|
Iwaranti
|
Iwaranti yonyaka ongu-1 enokwesekwa kobuchwepheshe bempilo yonke
|
Le yindawo ka Origin
|
China
|
Shipping Port
|
I-TIANJIN
|
EV Battery Assembly Line FAQS
How can the EV battery assembly line leverage automation to increase production speed?
I EV battery assembly line can leverage automation through the use of automated material handling systems and robotic arms. Automated guided vehicles (AGVs) in the EV battery assembly line can transport battery components precisely and quickly between workstations, reducing manual handling time. Robotic arms can perform tasks like cell picking and placing, ensuring consistent and rapid assembly operations. By integrating these automated elements, the EV battery assembly line minimizes bottlenecks and maximizes production speed.
What specific quality inspection methods are effective for the car battery assembly line?
For the car battery assembly line, automated optical inspection (AOI) systems and electrical testing equipment are highly effective quality inspection methods. AOI systems in the car battery assembly line can detect visual flaws in battery components, while electrical testing equipment verifies the functionality of battery modules and packs. Incorporating these inspection methods at multiple points in the car battery assembly line helps identify and address defects early, ensuring that only high - quality products are produced.
How does digital twin technology transform the car battery production line?
Digital twin technology transforms the car battery production line by enabling virtual simulation and optimization. Manufacturers can create a digital replica of the car battery production line and test different production scenarios, process improvements, and equipment configurations in a virtual environment. This allows for more informed decision - making regarding the car battery production line, reduces the risk of disruptions during actual production changes, and facilitates continuous improvement of the line's efficiency and quality.
What are the key aspects covered by the warranty for EV battery assembly line equipment from Xingtai Shuoding Trading Co., Ltd.?
The warranty for EV battery assembly line equipment from Xingtai Shuoding Trading Co., Ltd. covers several key aspects. It includes a 1 - year period during which any defective parts due to manufacturing faults in the EV battery assembly line equipment will be repaired or replaced. Additionally, the company offers whole - life technical support for the EV battery assembly line equipment, ensuring assistance for any technical issues throughout its lifespan.
In what ways can the equipment from Xingtai Shuoding Trading Co., Ltd. be customized for a car battery production line?
The equipment from Xingtai Shuoding Trading Co., Ltd. can be customized for a car battery production line in multiple ways. The company's experts can design and manufacture equipment that fits the specific assembly line configurations, production volumes, and quality standards of a car battery production line. Whether it's adjusting the size of machinery, integrating specific production functions, or ensuring compatibility with existing car battery production line setups, customization options are available to meet diverse customer needs.